Get uniform results with professional plastic extrusion techniques
Get uniform results with professional plastic extrusion techniques
Blog Article
Understanding the Basics and Applications of Plastic Extrusion in Modern Production
In the realm of modern production, the method of plastic extrusion plays a critical duty. Unraveling the principles of this procedure exposes the real convenience and potential of plastic extrusion.
The Fundamentals of Plastic Extrusion Process
While it may show up complex, the basics of the plastic extrusion procedure are based on relatively uncomplicated principles. It is a production process in which plastic is thawed and then formed into a constant account through a die. The plastic extrusion procedure is extensively made use of in various markets due to its efficiency, cost-effectiveness, and flexibility.
Various Kinds Of Plastic Extrusion Methods
Building upon the standard understanding of the plastic extrusion procedure, it is needed to check out the different techniques associated with this production technique. Both primary techniques are profile extrusion and sheet extrusion. In account extrusion, plastic is thawed and developed into a continuous profile, frequently used to create pipelines, poles, rails, and home window structures. On the other hand, sheet extrusion develops big, flat sheets of plastic, which are normally further refined into products such as food packaging, shower curtains, and car components. Each technique calls for specialized machinery and specific control over temperature and pressure to make sure the plastic maintains its form throughout cooling. Understanding these methods is key to using plastic extrusion effectively in modern-day manufacturing.
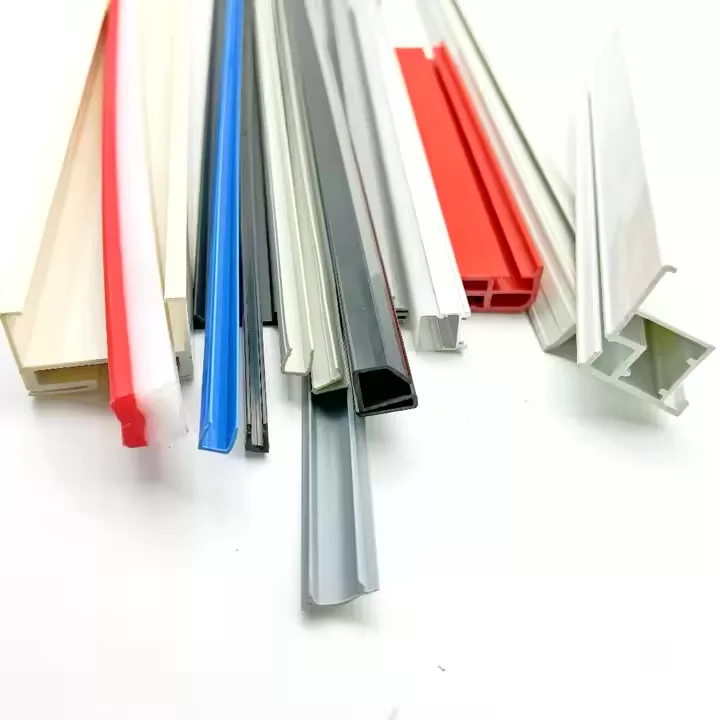
The Duty of Plastic Extrusion in the Automotive Market
An overwhelming bulk of components in modern vehicles are products of the plastic extrusion procedure. This procedure has actually reinvented the automobile market, changing it into a much more efficient, economical, and adaptable production market. Plastic extrusion is largely utilized in the production of numerous automobile parts such as bumpers, grills, door panels, and control panel trim. The procedure supplies an attire, regular result, allowing manufacturers to create high-volume parts with great accuracy and minimal waste. The agility of the extruded plastic components contributes to the total decrease in lorry weight, enhancing fuel effectiveness. Furthermore, the longevity and resistance of these parts to warmth, cold, and effect boost the durability of cars. Hence, plastic extrusion plays a critical duty in automotive manufacturing.
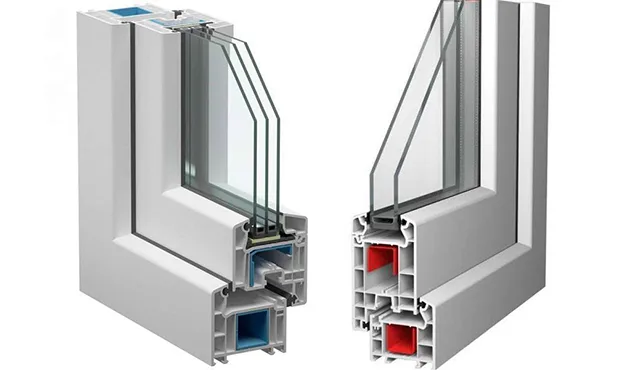
Applications of Plastic Extrusion in Consumer Item Production
Beyond its significant effect on the vehicle industry, plastic extrusion verifies equally effective in the realm of customer goods making. The convenience of plastic extrusion enables manufacturers to design and produce complicated shapes and sizes with high precision Resources and effectiveness. The adaptability, adaptability, and cost-effectiveness of plastic extrusion make it a preferred selection for lots of customer products suppliers, adding considerably to the sector's growth and technology.
Environmental Impact and Sustainability in Plastic Extrusion
The prevalent usage of plastic extrusion in manufacturing invites examination of its environmental ramifications. As a process that often utilizes non-biodegradable products, the ecological influence can be significant. Energy intake, waste manufacturing, and carbon discharges are all concerns. Market innovations are enhancing sustainability. Efficient equipment lowers energy usage, while waste administration systems recycle scrap plastic, lowering he said basic material demands. In addition, the advancement of biodegradable plastics uses a much more eco-friendly alternative. Regardless of these improvements, better development is required to mitigate the ecological footprint of plastic extrusion. As society leans in the direction of sustainability, producers should adapt to remain sensible, emphasizing the value of continual research study and development in this field.
Conclusion
In conclusion, plastic extrusion plays a crucial duty in modern-day production, especially in the auto and consumer products industries. Recognizing the fundamentals of this use this link procedure is key to maximizing its advantages and applications.
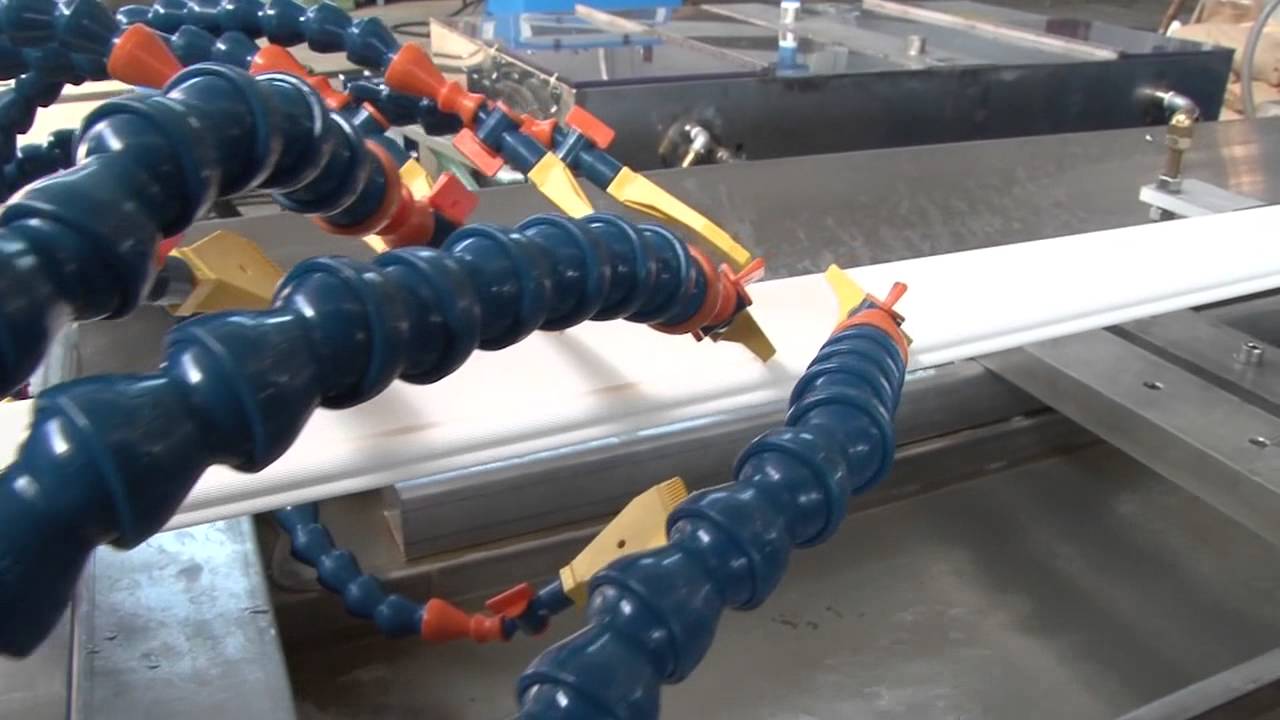
The plastic extrusion process is extensively used in various sectors due to its cost-effectiveness, efficiency, and versatility.
Structure upon the basic understanding of the plastic extrusion procedure, it is essential to check out the various methods included in this production technique. plastic extrusion. In comparison, sheet extrusion produces large, level sheets of plastic, which are commonly additional processed right into items such as food packaging, shower drapes, and auto parts.An overwhelming bulk of parts in modern-day vehicles are products of the plastic extrusion procedure
Report this page